
The major ways I have seen are listed below: There are several ways to set cost, both explicit and implicit costs, in a cost optimizer. Implicit costs like this are more difficult to estimate than explicit costs because they can’t be found in any invoice or real cost the company pays, but comes down to the goals and objectives of the company. For a cost optimizer to appreciate that not stocking out is important to the company, and for an appreciation of how important it is to meet this demand, a cost optimizer requires a cost associated with an unmet demand, which is then traded off against the costs of ordering, keeping items in stock, transporting items, etc. That customer may purchase another item from the company’s offering, or may move on to a different company’s item, and in the latter case the first company has lost the profit and goodwill of that potential sales had they been in stock. The customer goes away, and no sale is made on that item. When a company fails to meet a demand, there is no accounting entry for this. These are costs that the company does not actually pay out but are implicit in the activities of the business. Penalty costs are an example of an implicit cost. Estimating these costs is tricky, and surprisingly, there is generally not a group inside a company that can help with this cost estimation. They are paid out by the company, but must be aggregated because it’s not feasible to enter the costs for every single shipment into the model. Before we go into the cost development methods its important to review the distinction between explicit costs versus implicit costs.Įxplicit costs are the costs that the company actually incurs, these would include things like transportation costs and storage costs.

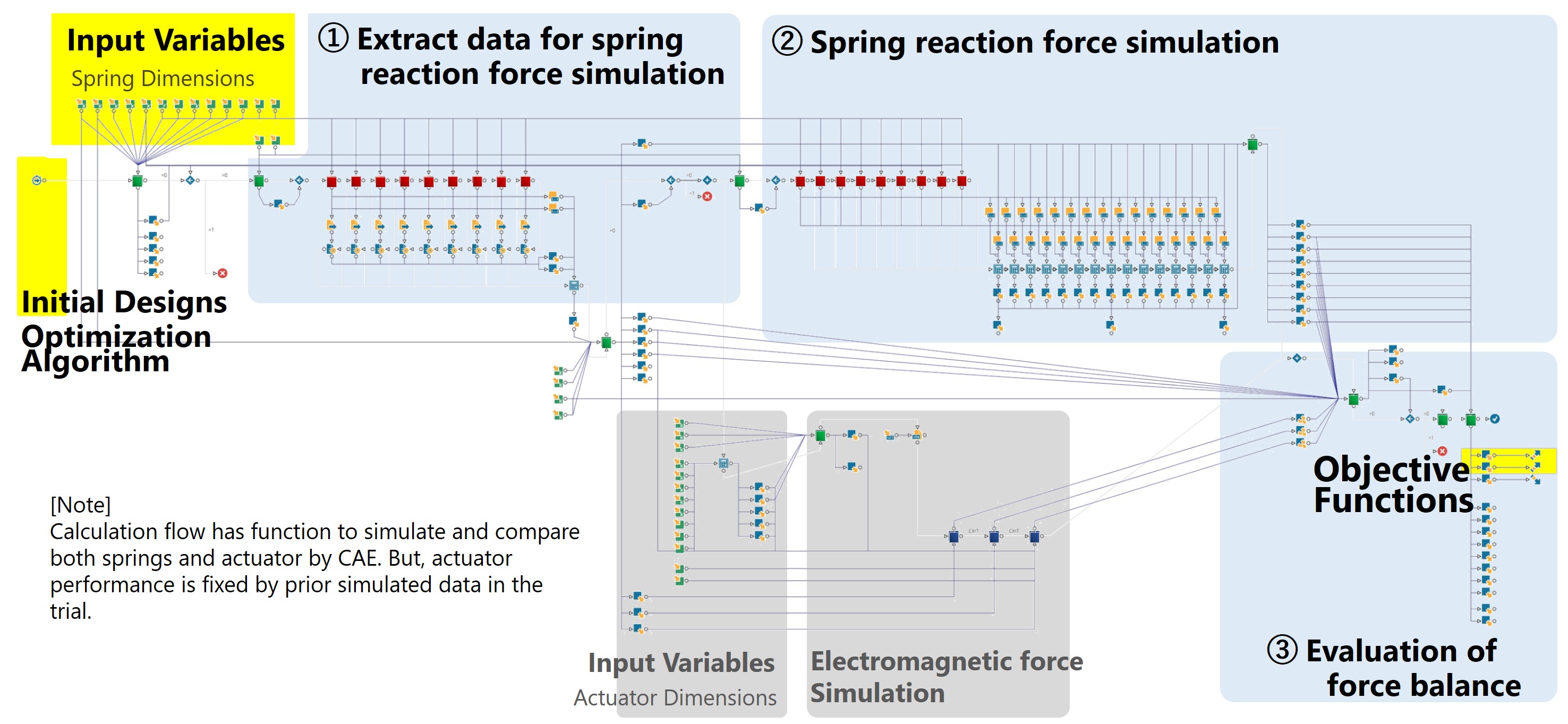
During the software selection stage, this tends to be covered from a surface level, but it is probably the most important element to investigate thoroughly before engaging in cost optimization implementations. The graphic above describes major elements of cost optimization that applies to supply planning.Ĭost optimizers use both explicit and implicit costs to generate the plan. In working on a number of cost optimization accounts over the years and in conferring with other individuals who have worked in the area for some time, I have come to a conclusion regarding how costs are set in both supply planning and production planning implementations.
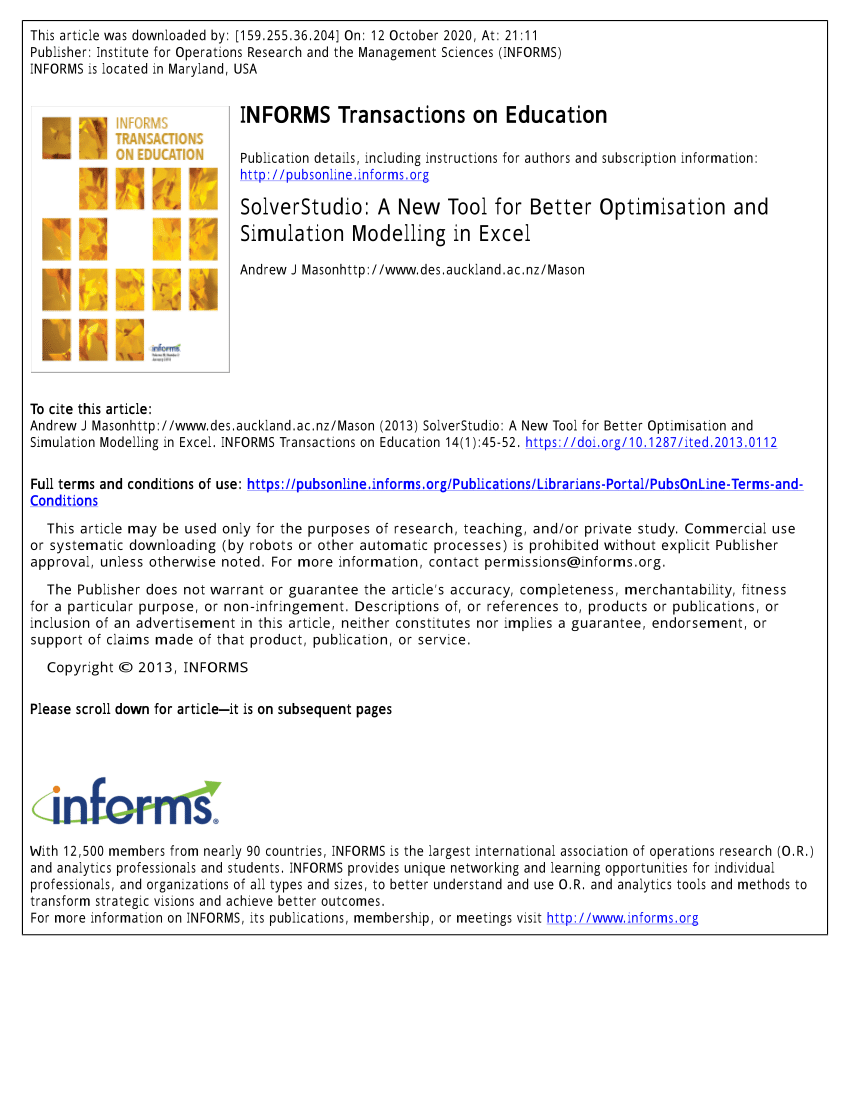
How does this compare to inventory optimization and multiechelon systems?.

What are the implications to how costs are set?.What are actual costs versus what is normally used?.What are implicit versus explicit costs?.
